Story at a glance:
- The preconstruction phase of every project is a critical time for ensuring you avoid rework.
- Integrated cloud technologies offer increased productivity and streamlined processes.
Buildings are currently responsible for 39% of global energy related carbon emissions: 28% from operational emissions and 11% from materials and construction. As we collectively look to reduce our carbon footprints, many in the AEC space are looking for ways to build more sustainably. There have been great advancements in this area with a number of initiatives and resources focused solely on green building practices.
While not every construction firm may have sustainability practices in place yet, there are ways everyone can make a difference. Utilizing the right technology can not only boost productivity on a project, but it can also help minimize its environmental impact. Let’s take a closer look at three types of technology (some of which you may already be using) that can help reduce emissions: preconstruction technologies, integrated cloud solutions, and emerging technologies.
1. Preconstruction Technologies
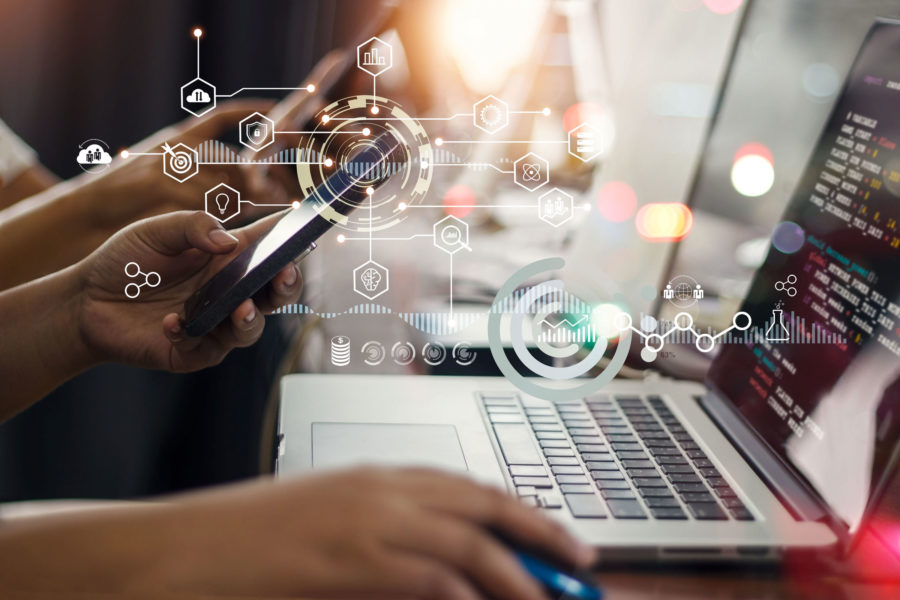
Photo courtesy of Sage
The preconstruction phase is critical in setting a project up for success. Having accurate estimates and models can help ensure the job is right the first time, eliminating excess waste and rework. Estimating, building information modeling (BIM), and prefabrication are a few technologies that can have a big impact on preconstruction.
Estimating
Estimating software helps construction companies create more accurate estimates in less time. This not only helps ensure you are pursuing the right projects at the right price, but it saves time and resources by automating the estimation process. This can save time and effort and eliminate extra trips to the job site.
BIM
BIM creates a digital representation that communicates the physical and functional characteristics of a project. It provides a detailed 3D model of the building before construction begins. 3D BIM includes information about the physical geometry and spatial relationships of the building’s components, which aids in clash detection so teams can make adjustments early in the design phase to avoid potential problems in the building phase of a project.
4D BIM adds the element of time, including information about the construction schedule, which allows for more streamlined planning and scheduling of construction activities. 5D BIM adds the element of cost to the 3D and 4D models. This includes information about the price of materials, labor, and other resources needed to complete the project. This helps create more accurate cost estimates and helps optimize resource management.
BIM allows all project stakeholders to collaborate and communicate more efficiently, making it easier for teams to identify any potential issues or design flaws before building begins. This helps streamline the design, build, and operations phases, which can help deliver more sustainable project outcomes. BIM provides accurate and detailed information about a building’s performance, including energy consumption, water usage, and waste production, which can be used to make more informed decisions in an effort to reduce a building’s environmental impact.
Prefabrication
Prefabrication involves the off-site manufacturing of building components that are later assembled on-site. BIM aids in this process as it enables the creation of accurate and detailed designs that can be used to create prefabricated components off-site. While prefabrication isn’t exclusively a preconstruction process, and can be completed during the building phase, I’ve included it here since its use would be determined in the preconstruction and planning process.
During prefabrication units are assembled in factory-like settings using machines and automated technologies. This enables greater quality control and delivers faster production and cost savings for both on-site labor and building materials.
Prefabrication can also help offset a project’s environmental impact. When units are created in bulk, manufacturers can utilize more of the building materials with less scraps left over. Plus all units are also inspected before being shipped, minimizing the waste that can come from defects and mistakes. Additionally, many prefabrication facilities have implemented recycling programs to further minimize waste. Prefabrication also helps reduce the time spent driving to and from the job site, lowering carbon emissions by streamlining transportation, and also reducing noise and dust on the job site.
2. Integrated Cloud Solutions
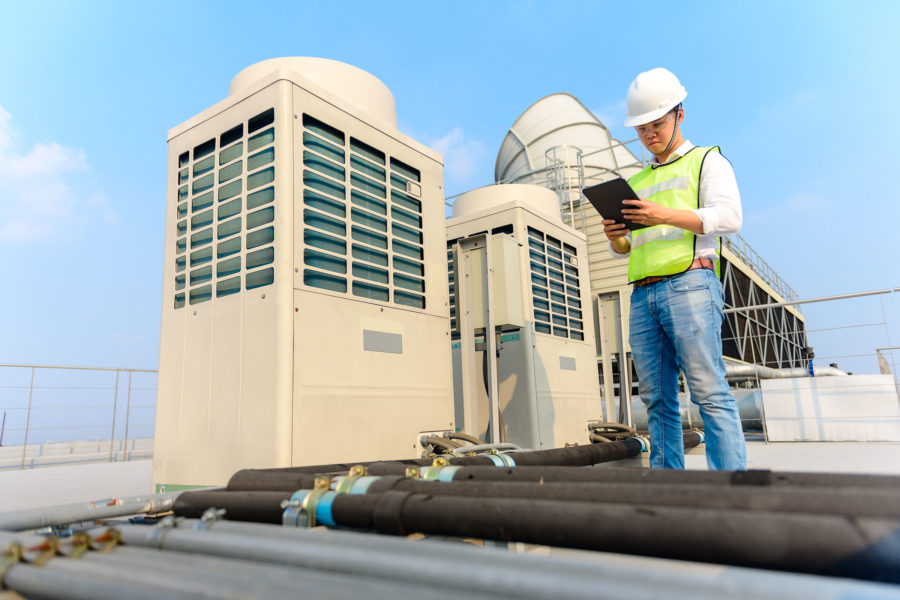
Photo courtesy of Sage
The use of integrated cloud technologies delivers a host of benefits, from increased productivity and streamlined processes to improved collaboration and real-time access to data, which aids in better decision making. But the use of integrated cloud solutions can also help us build more sustainably.
It is critical to ensure all of your technology solutions are integrated. Integrated solutions connect all of your data, eliminating the need for redundant and error-prone duplicate data entry. When all systems are connected you can also take advantage of reliable customized dashboards, and monitoring and alert systems. This way you always have a real-time snapshot of a project’s progress, and an automated system can track for specific conditions to be met and immediately alert the right people. This can help you course correct before costly and wasteful errors are made during the building process.
Aside from your traditional back-office and field tools, there are a growing number of building automation systems and tools that can assess the environmental impact of building materials and also provide real-time data on building energy consumption and other sustainability metrics. Utilizing connected technologies to create smart buildings can help sustainability efforts in the operations phase of a building’s lifecycle. Sensors can help regulate things like lighting and temperature to reduce energy usage and also detect leaks or other inefficiencies, enabling more prompt and efficient repairs.
3. Emerging Technologies
Smart buildings are becoming more common in new construction as is the use of emerging technologies such as 3D printing, virtual reality (VR) and augmented reality (AR), and artificial intelligence (AI). These technologies deliver a new level of precision to the building process and can significantly reduce waste and rework.
3D Printing
Similar to prefabrication, 3D printing allows for building components to be created with the exactness of a machine, reducing the amount of waste created in the building process. 3D printing technologies can even be utilized on-site, reducing the need for transportation of building components. 3D printing also enables the use of more eco-friendly and recycled materials to create building components.
Virtual and Augmented Reality
Virtual and augmented reality provide many of the same advantages of BIM modeling but take it to a whole new level. Virtual reality provides a simulated immersive experience in a virtual world, while augmented reality adds virtual components to a real-world setting; think walking a construction site and seeing the completed project right before your eyes. Both aid in better visualization of a construction project and help identify potential issues before construction begins, reducing the likelihood of errors and eliminating excess waste.
Artificial Intelligence
The use of AI in construction can help automate processes with machine-like consistency and accuracy. When it comes to reducing the environmental impact of construction, one area AI can have an impact is waste management. Technologies have been developed to help sort construction waste in an effort to increase the recycling and reuse of materials, including the use of robotics to reclaim waste construction wood.
AI can also help in sustainable building maintenance. AI can learn a smart building’s behavior over time and actually predict when a building needs to be maintained or when components need to be serviced. This helps streamline maintenance and can help reduce trips to the building site.
Conclusion
Technology is revolutionizing the way we plan, construct, and operate our buildings. Advances in preconstruction, cloud, and emerging technologies have opened up a new world of possibilities when it comes to increasing efficiencies and reducing project waste and rework. As technology continues to advance we will see even more opportunities to optimize the project lifecycle and further minimize construction’s environmental impact.