Story at a glance:
- Structural insulated panels, or SIPs, are a type of lightweight, high-performance composite paneling used to construct energy-efficient walls, floors, roofs, and foundation systems.
- Most SIPs feature either a polyurethane, polystyrene, or polyisocyanurate foam insulation core sandwiched between two OSB sheathing panels.
- The benefits of using SIPs in construction include reduced operating costs, faster construction times, improved indoor air quality, and more.
Structural insulated panels, or SIPs, have become increasingly popular over the last few decades, in large part due to their versatility and potential for energy savings. With SIPs becoming increasingly common, though, it’s important to actually know precisely what they are and why they work the way they do—how they contribute to a structure’s overall energy efficiency.
In this article we’ll cover the basics of SIPs, including what they are and how they’re used, their components, as well as their benefits and disadvantages compared to traditional stick-framed structures.
What are SIPs?
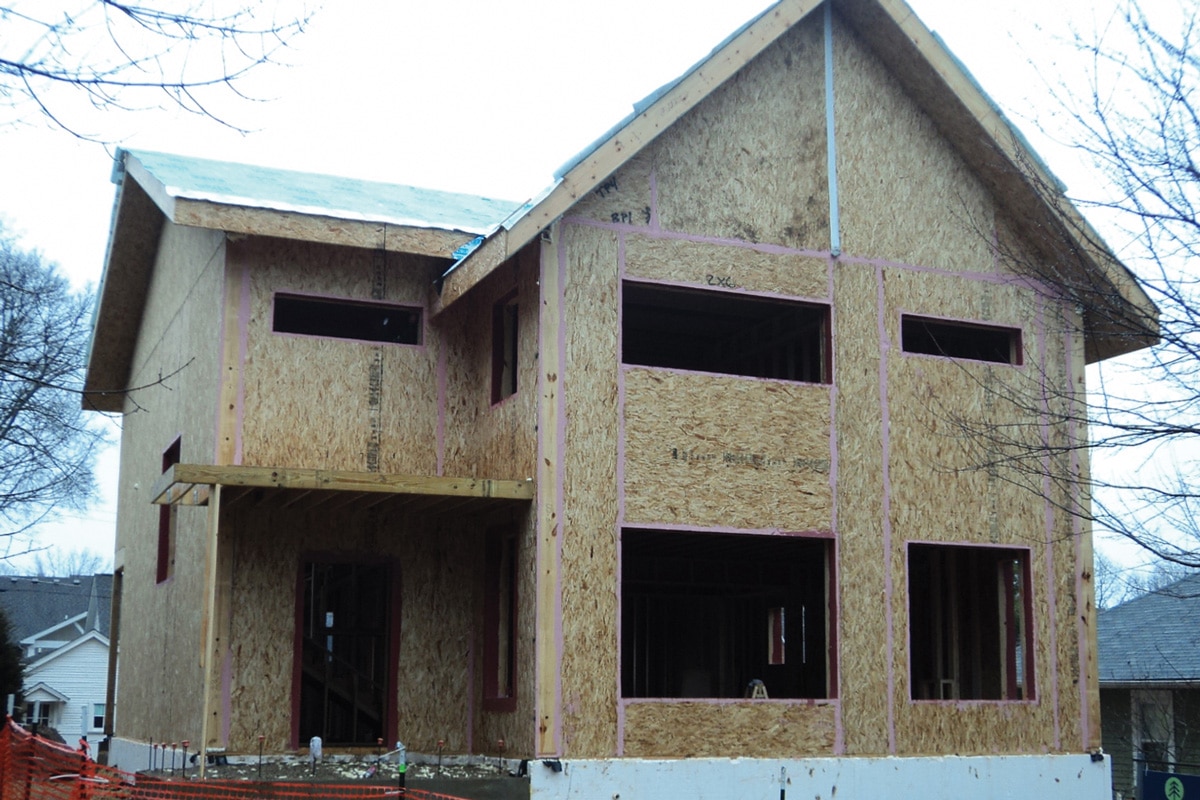
A structural insulated panel is a type of high-performance composite paneling that is frequently used to create walls, floors, roofs, and foundations for residential and light construction projects. Photo courtesy of FischerSIPS
Structural insulated panels (SIPs) are a type of lightweight, high-performance composite paneling used in residential and light construction projects to create walls, floors, roofs, and even foundation systems. SIPs are designed to share the same structural properties as traditional I-beams or I-columns, with the insulated core acting as the web and the sheathing fulfilling the function of the flanges.
In the United States SIPs are available in sizes ranging from 4 feet to 24 feet in width (though longer widths may be requested in special circumstances), typically measure 8 to 9 feet tall, and range between 4 to 12 inches in thickness. SIPs are almost always prefabricated off-site in a highly-controlled, low-waste environment before they are then shipped to the job site and installed.
As a general rule smaller SIPs are easier to work with and may be installed manually by hand, but create more opportunities for thermal bridging between panels—larger SIPs, on the other hand, create a tighter thermal envelope but are also heavier and typically require the aid of a forklift or crane to be fitted into place.
Anatomy of a SIP
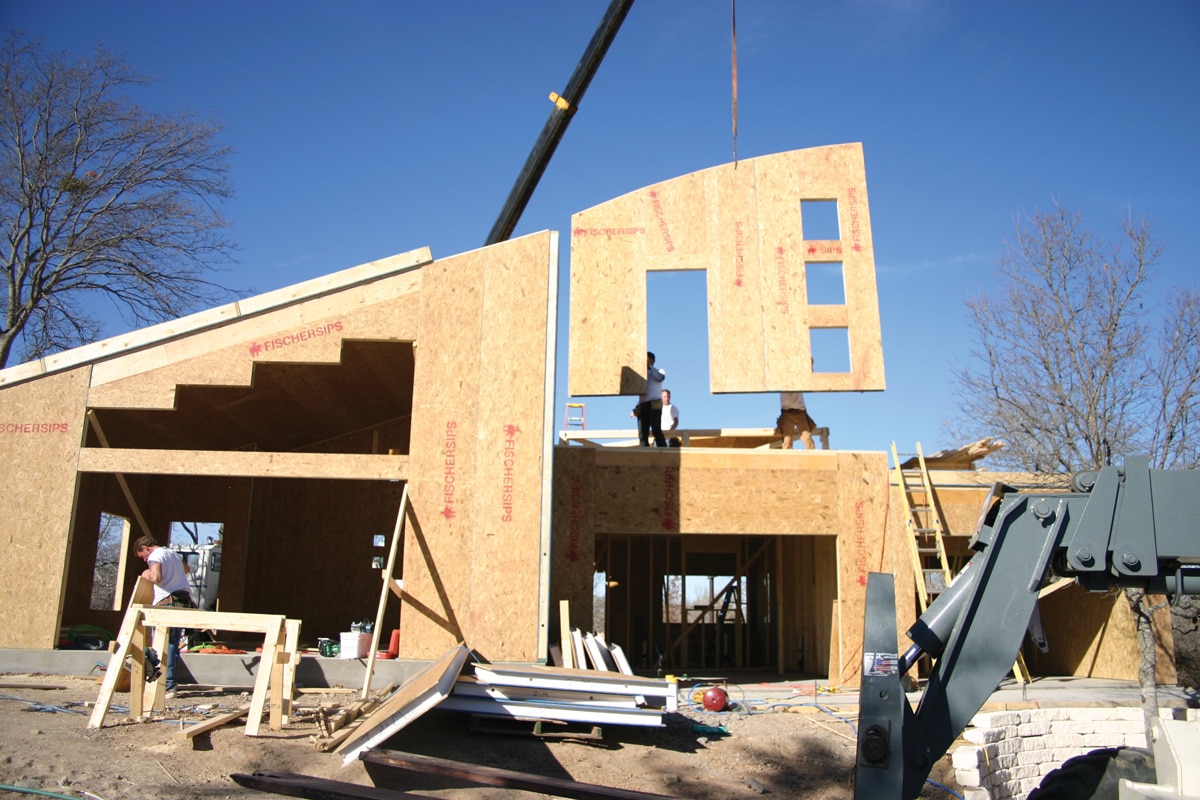
A SIP consists of two sheathing panels encasing an insulated foam core, with splines separating each SIP from another. OSB is the most common sheathing material for SIPs, with polyurethane, polystyrene, and polyisocyanurate rigid foam being the most popular insulations. Photo courtesy of FischerSIPS
While the exact material components of SIPs may vary between manufacturers, all possess the same basic anatomy and include three key elements: sheathing/panels, an insulated core, and a spline.
Sheathing
Both the outward- and inward-facing sides of an SIP are referred to as sheathing and provide the SIP with its structural capacity. Most SIPs use oriented strand boards (OSB) for their sheathing, as OSB—a sort of upgraded version of traditional plywood—is engineered to provide maximum strength and durability. High-grade OSB sheathing gives each SIP the strength to maintain a vertical point load of just over a ton and a total vertical uniform load of two tons.
While it is the market standard, OSB is not the only option available for SIP sheathing—plywood, for example, is also used, with pressure-treated plywood panels being the favored option for constructing below-grade foundation walls. Other potential materials include aluminum, steel, stainless steel, magnesium oxide, fiber-cement, and fiber-reinforced plastic.
Insulated Core
The insulated core of an SIP is sandwiched between the two sheathing panels and is most commonly constructed from the following types of insulation:
- Extruded polystyrene (XPS) foam. XPS is a strong, lightweight, and water-absorption-resistant type of closed-cell rigid foam insulation that typically possesses an average R-value of R5 per inch.
- Expanded polystyrene (EPS) foam. EPS foam is very similar to XPS foam but is lighter, thicker, and has an average R-value of R4 per inch.
- Graphite polystyrene (GPS) foam. A type of high-performance, closed-cell insulation with a typical R-value between R4.5 and R5 per inch.
- Polyurethane (PU) foam. PU insulation is available as either an open- or closed-cell foam, with the closed-cell variety being both moisture- and mold-resistant; open-cell PU foam has an average R-value of R3.5 while closed-cell PU foam has an R-value between R6.5 and R7 per inch.
- Polyisocyanurate (PIR) foam. PIR or polyiso is a kind of thermoset plastic insulation produced as a closed-cell, rigid, continuous foam board; like PU foam, PIR has one of the highest R-values on the market and averages between R6 and R6.5 per inch.
For projects looking to drastically reduce their overall environmental impact and reliance on synthetic man-made materials, natural agricultural fiber or plant-based polyurethane rigid foam may be used to construct the core instead.
Spline
SIPs also feature a spline, which serves as a connector piece between individual SIPs. Historically these splines have been constructed from dimensional lumber, but seeing as traditional dimensional lumber acts as a thermal bridge and therefore reduces insulation value, other solutions—such as using a composite spline, insulated lumber, or overlapping OSB panels—are favored when designing for energy-efficiency.
Benefits of SIPs

Building with SIPs is sustainable, makes for shorter construction times, and drastically improves a structure’s overall energy-efficiency. Photo courtesy of FischerSIPS
There are many benefits of using SIPs in the construction of residential and commercial structures, including:
Energy Efficiency
As with any insulation product the main benefit of SIPs is the energy-efficiency that comes as a result of their excellent thermal performance. On average SIPs reduce heating and cooling energy loads by at least 50% compared to traditional timber-framed structures, resulting in much lower operating costs and significant monthly savings.
Aside from their high insulative capacity and lack of thermal bridges, properly installed SIPs also guarantee energy-efficiency by being incredibly resistant to air leakage. Air leaks account for between 25 and 40% of the energy used to heat and cool a building and drastically reduce the effectiveness of other energy-saving measures, according to the experts at Energy Star—but because SIPs are prefabricated in a controlled environment, they fit snug against one another and virtually eliminate the possibility of air entering through gaps or cracks.
“Because SIPs are more airtight than your typical structure, you don’t have a lot of air passing in and out of your house,” Damian Pataluna, owner of FischerSIP, previously told gb&d. This translates to less energy waste and drastically reduced heating and cooling loads, making SIPs an ideal choice for projects seeking LEED, Passive House, or Net Zero Energy certification.
Improved Indoor Air Quality
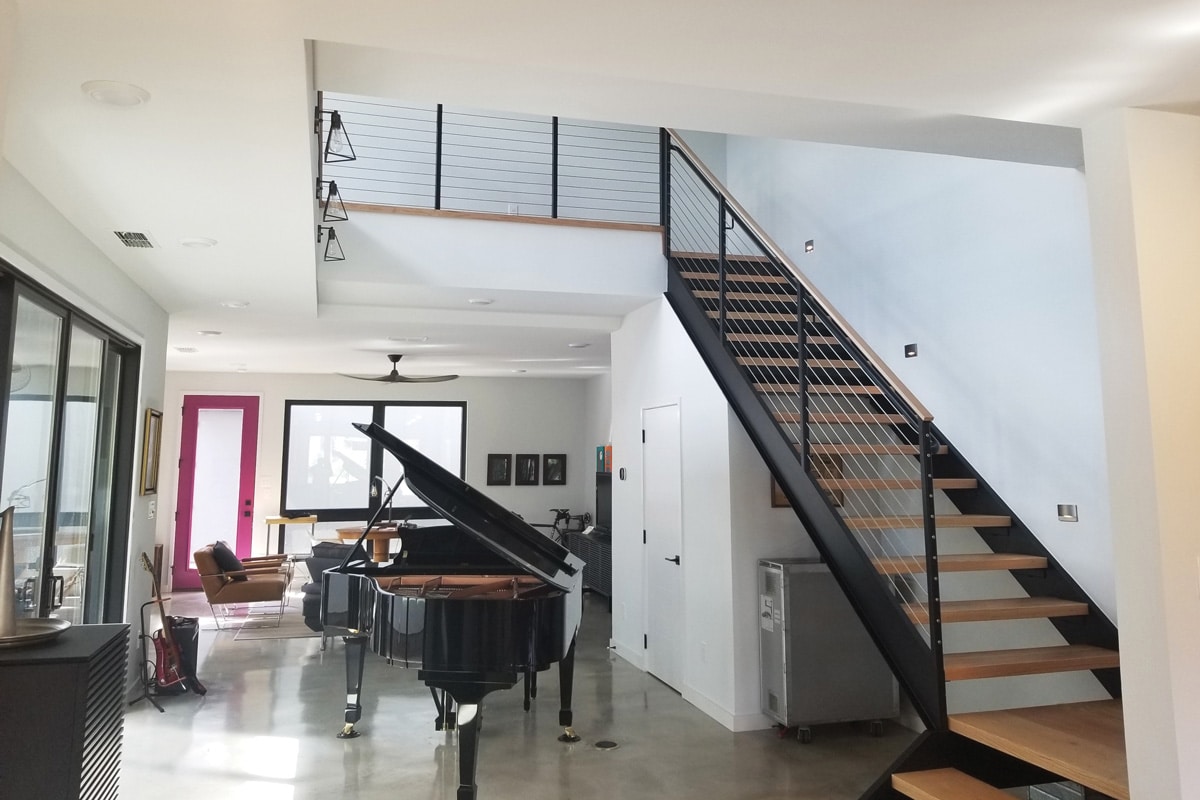
The airtight building envelope created by SIPs helps ensure that all indoor air enters through a dedicated ventilation system that filters out pollutants. Photo courtesy of FischerSIPS
Another often overlooked benefit of SIPs is their role in improving indoor air quality. By reducing the amount of air leakage into and out of a building’s envelope, SIPs help ensure that air circulation only occurs through controlled ventilation systems that filter out allergens, dust, and other contaminants that might otherwise pollute interior spaces. Because they are designed for superior airtightness and to minimize or eliminate the thermal bridging that so often befalls timber-framed structures, SIPs also greatly reduce the risk of condensation buildup that might lead to potentially hazardous mold or mildew growth.
Environmental Sustainability
Because SIPs help improve a building’s energy-efficiency, they also help prevent a significant amount of GHG emissions from being produced and therefore reduce a project’s overall environmental impact. And even though SIPs generate emissions during the manufacturing process, the energy savings they provide effectively cancel out those emissions in just under four years, according to SIPA.
Speaking of manufacturing, SIPs also help promote environmental sustainability by leveraging prefabrication technology to their advantage, as such methods require fewer material resources and create less construction waste. Building envelopes that use OSB SIPs, for example, are only 3 to 5% lumber, whereas buildings that feature traditional 2×6 framing are between 22 and 24% lumber. What’s more, OSB is typically produced from sustainably harvested new growth trees rather than old growth trees.
Less Labor & Faster Construction Times
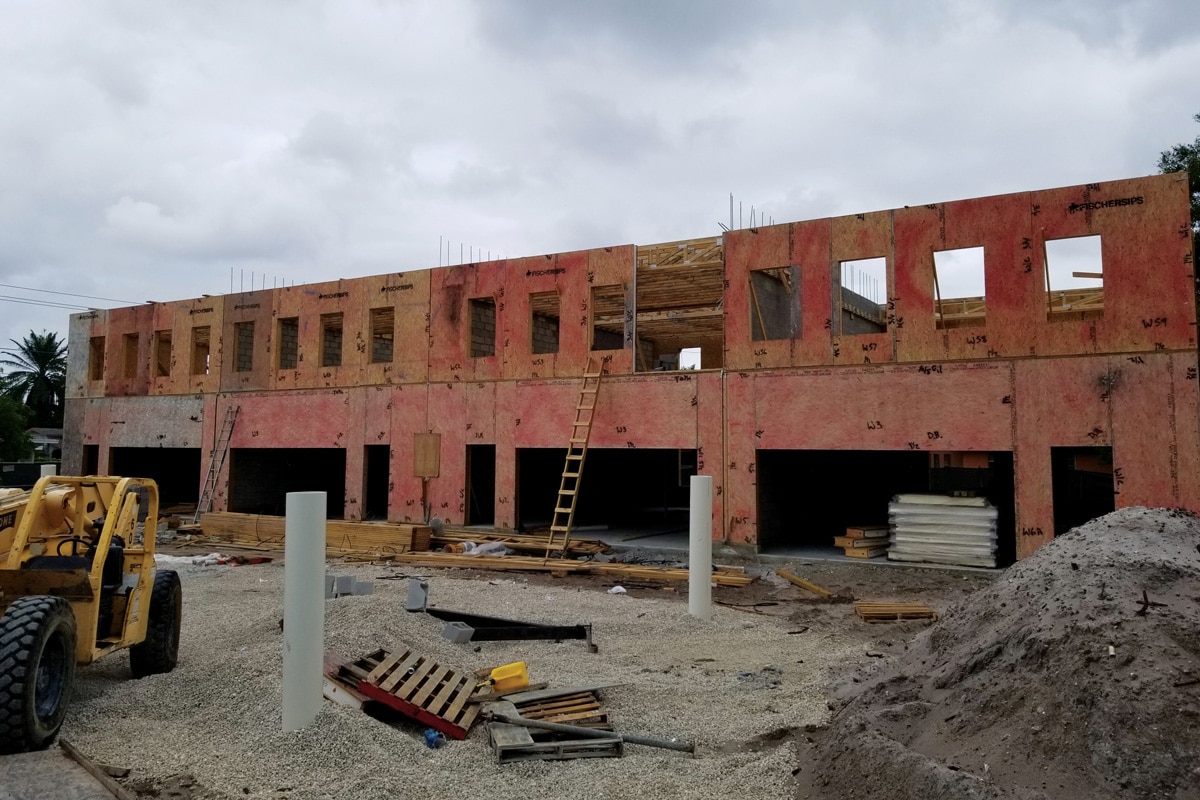
Because SIPs are prefabricated off-site and then shipped to the job site, they can drastically reduce construction times. Photo courtesy of FischerSIPS
Another benefit of SIPs—and really any prefabricated building material—is that they help reduce on-site construction times and labor requirements. “A lot of time on job sites you see guys out there scratching their heads, trying to figure out how to cut a complex angle and make it work,” says Pataluna. “Or you may have a situation where it’s dangerous because it’s high in the air. If we can get it figured out in a safe factory setting and then ship it out to a jobsite where it’s pre-assembled on the ground, think of the time-saving safety factors that are involved with that.”
SIPs are capable of reducing on-site labor needs by as much as 55%, according to a BASF Corporation time-motion study conducted by the RS Means unit of Reed Construction.
Durability & Resiliency
Because they are intended for use as structural, load-bearing building components, SIPs offer the benefits of high strength and impressive durability. This is largely due to the fact that SIPs are structurally similar to traditional steel I-beams—the SIPs’ sheathing functions as the flange and allows it to resist most bending movement, while the rigid foam core acts as the web and allows it to effectively absorb shear force. All in all this design allows SIPs to evenly shoulder in-plane compressive loads of approximately two tons.
On average buildings constructed from SIPs are two-and-a-half times stronger than conventional stick-framed structures. This structural strength, combined with their general construction, also means SIPs are incredibly resilient and well-equipped to withstand extreme weather events—a growing concern as the effects of anthropogenic climate change worsen.
“The way SIPs are tied together with the long panel screws creates incredible sheer strength,” says Pataluna. “You won’t typically have situations where the trusses or individual pieces of sheeting can be ripped off the roof because the roof panels are one solid sheet inside and outside that are screwed down to the walls. You’d almost have to pick up the entire house to rip it off the foundation.”
Indeed, most SIPs are capable of withstanding 145 mile-per-hour winds without necessitating any additional tie downs, allowing them to weather even the strongest hurricanes and tropical storms.
Disadvantages of SIPs
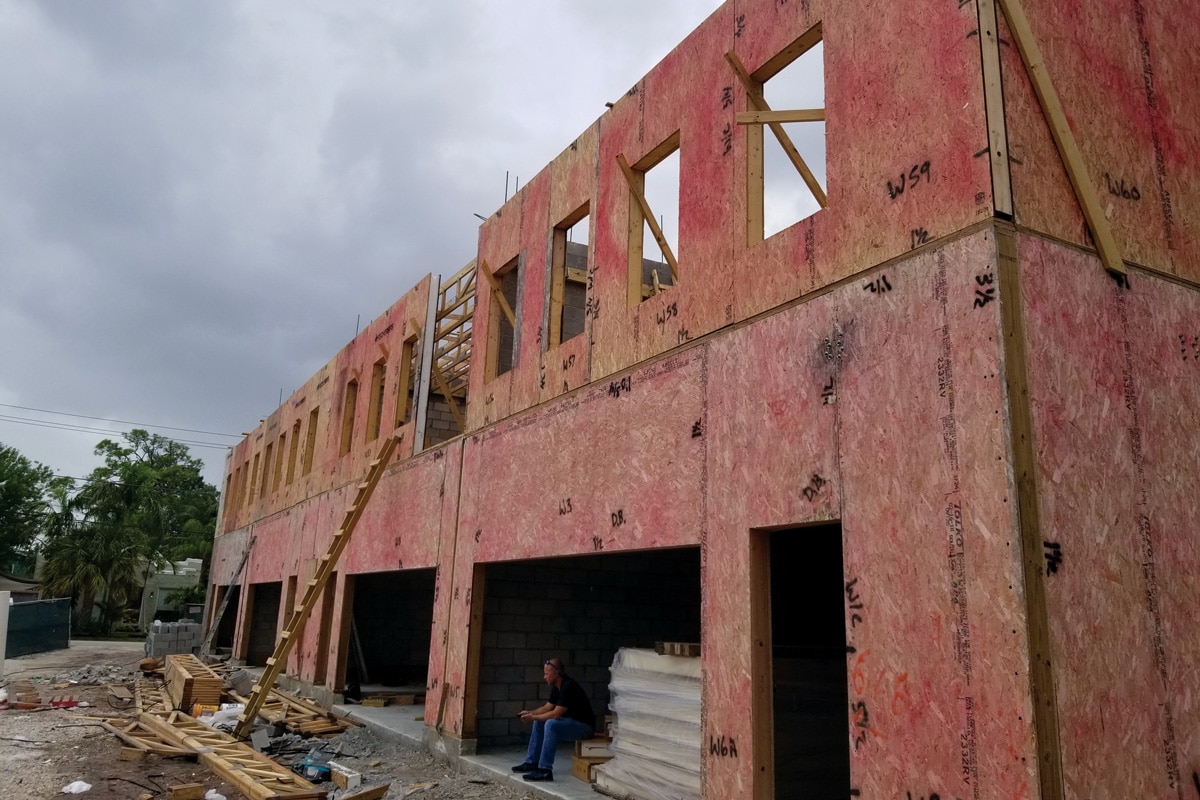
While extremely beneficial, SIPs tend to have higher up-front costs compared to traditional stick-framed structures, are susceptible to water damage, and are harder to modify on-site should the need arise. Photo courtesy of FischerSIPS
Like any building product, however, SIPs are not without their challenges and disadvantages—but most AEC experts agree that these potential drawbacks are outweighed by the numerous benefits SIPs provide.
Higher Up-Front Costs
While building with SIPs is one of the cheapest options for constructing high-performance, energy-efficient structures, SIPs still cost more than traditional stick-framed buildings—3 to 7% more, to be exact.
That said, the higher up-front costs of SIPs are completely justified given the amount they save property owners in energy-related operating costs. Prefabricating SIPs offsite also helps reduce a project’s overall construction and labor costs, which helps balance out the up-front purchasing cost even further.
Structural Creep
Unless their sheathing is made from steel or some other structural metal, SIPs—and all structural materials, for that matter—will suffer creep over time as a result of persistent mechanical stress. While a natural phenomenon, creep can eventually lead to SIP failure if it is not properly addressed.
Creep-mitigation design recommendations do exist, but these suggestions are based primarily on research regarding creep in SIPs featuring OSB-facing and either a polyurethane or EPS foam core—creep in SIPs composed of other, non-traditional materials may be more difficult to anticipate.
Susceptible to Water Damage
While not true of SIPs featuring water-resistant sheathing (e.g. fiber-reinforced plastic or fiber-cement), SIPs using OSB, plywood, aluminum, or steel panels are susceptible to water damage in the event of moisture intrusion and buildup. If left unchecked, this can lead to rotting, rusting, and/or mildewing of the SIP, all of which may compromise its structural integrity.
Fortunately this is an easy problem to avoid, as it simply necessitates the installation of a waterproof or water-resistant surface over the SIPs.
Harder to Modify Onsite
Because SIPs are prefabricated entirely off-site and then shipped to the job site as a finished product, they are much more difficult to modify on-site should any corrections or adjustments need to be made. Of course, the highly-controlled environment in which prefabricated SIPs are produced aims to minimize or completely eliminate the need for on-site modifications, but accidents and unforeseen changes do happen.